Why Small Mistakes in LTL Shipping Can Cost You
Less-than-truckload (LTL) freight shipping is a smart choice for businesses that don’t need to book an entire truckload. It allows shippers to move freight efficiently while keeping costs manageable. However, even minor mistakes in the shipping process can lead to unexpected fees, higher LTL freight rates, shipment delays, and dissatisfied customers.
Many businesses unknowingly miscalculate freight class, improperly label freight shipments, or fail to choose the right freight carriers—all of which can impact pricing and transit times. In this guide, we’ll cover the most common LTL shipping mistakes and provide practical solutions to help you streamline your shipping process, reduce costs, and avoid unnecessary headaches.
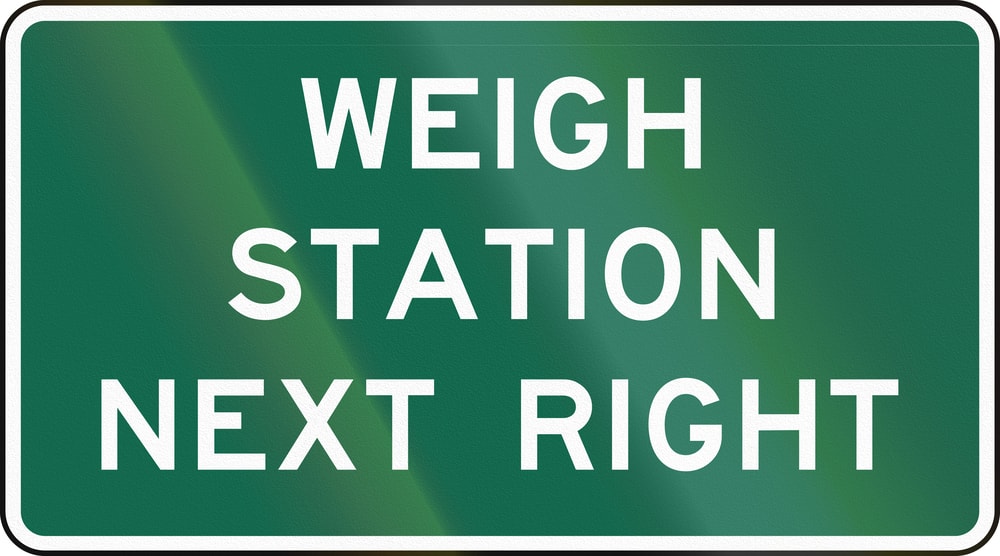
Mistake #1: Incorrect Freight Class & Weight
One of the most common and costly mistakes in LTL freight shipping is misclassifying freight. LTL carriers rely on freight class to determine shipping rates, factoring in weight, density, stowability, and handling requirements. If your freight is classified incorrectly, you could face costly reclassification fees, shipment delays, or even rejected loads.
How to Avoid It
-
Use an accurate freight class chart – Refer to NMFC (National Motor Freight Classification) standards to ensure you’re using the correct freight class for your shipment. Different classifications come with different pricing, so accuracy is key.
-
Weigh and measure shipments correctly – Small errors in dimensions or weight can lead to unexpected rate adjustments. Always use certified scales and precise measuring tools.
-
Double-check density calculations – Density plays a major role in determining freight class. Use a freight class calculator to verify that your shipment’s weight-to-volume ratio aligns with the correct classification. Higher-density freight often falls into a lower (cheaper) class, so optimizing packaging can help reduce costs.
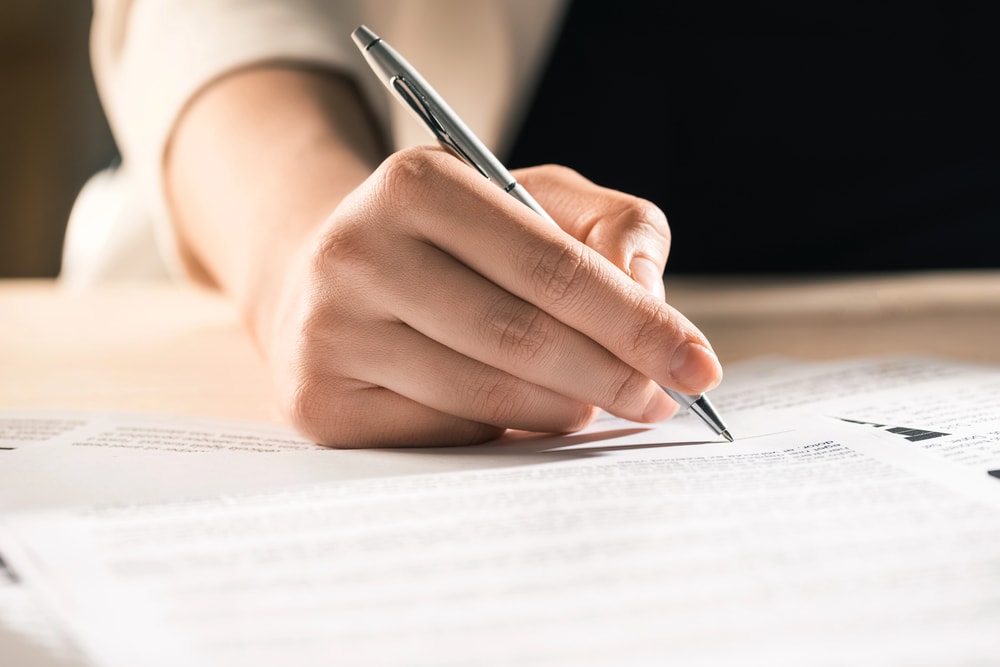
Mistake #2: Incomplete or Incorrect Bill of Lading (BOL)
The Bill of Lading (BOL) is the most critical document in LTL freight shipping. It serves as a contract between the shipper and the carrier, outlining essential shipment details. Missing or inaccurate information—such as incorrect freight classifications, weight, or handling instructions—can lead to delays, rerouted shipments, or unexpected fees. For businesses shipping multiple shipments or different commodities, ensuring the BOL is correctly filled out is even more important.
How to Avoid It
-
Verify pickup and delivery addresses – Errors in address details can result in missed delivery windows, causing delays and additional re-consignment fees. Always double-check the accuracy of both the origin and destination.
-
Include precise shipment details – The BOL must accurately reflect freight class, total weight, and any special handling requirements, such as hazardous materials. Incorrect information can lead to costly adjustments or rejected shipments.
-
Use a digital BOL – Digital BOLs help eliminate manual errors, streamline processing, and improve tracking. They also provide a clear, accessible record in case of disputes.
-
Account for total cubic feet – Some freight trucks price shipments based on volume rather than weight. Ensure your BOL includes the correct dimensions, especially if you’re shipping large or irregularly shaped freight.
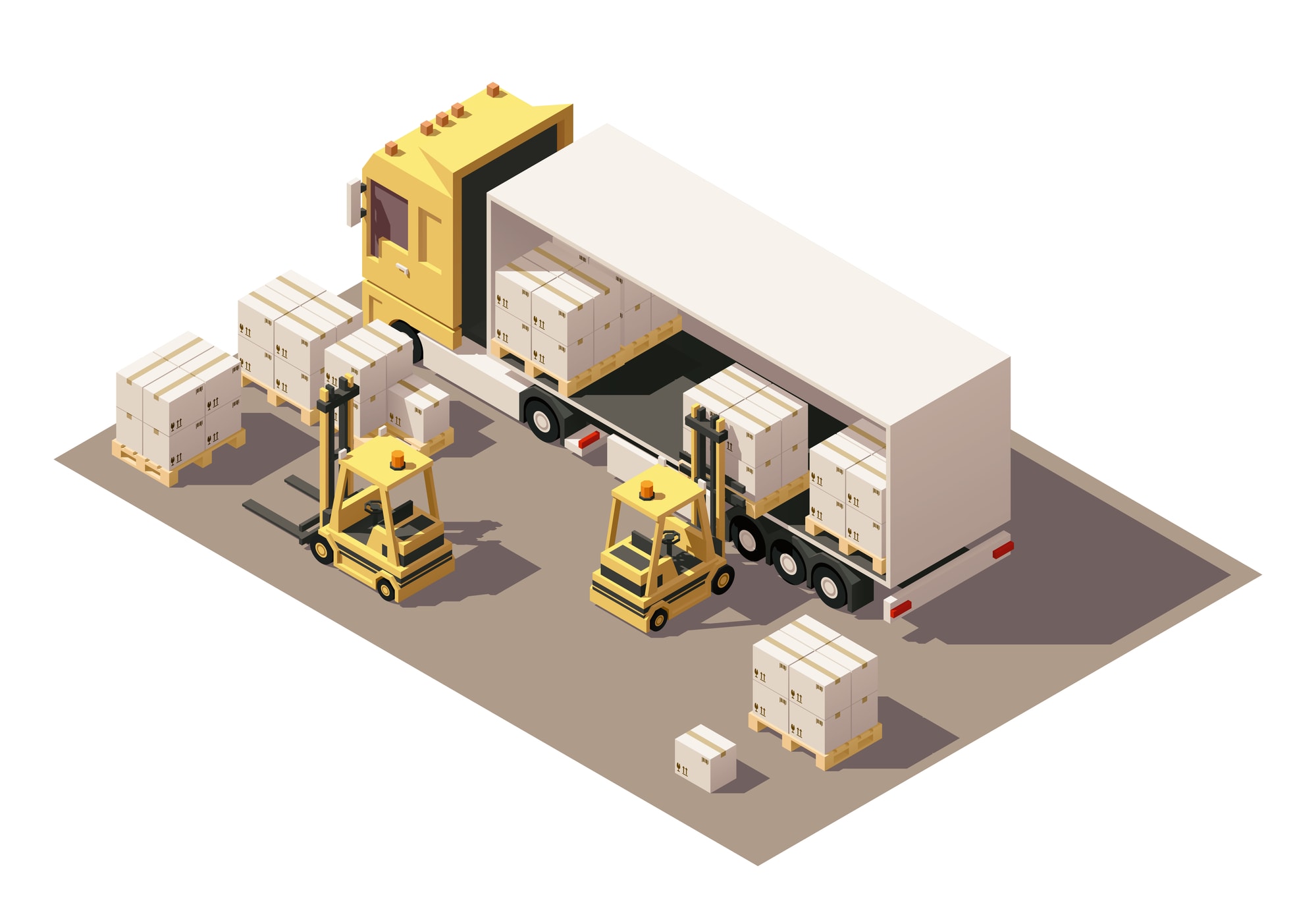
Mistake #3: Insufficient Packaging & Palletizing
Unlike other freight that fills an entire truck, less-than-truckload (LTL) shipments are combined with individual shipments from multiple shippers. This means your freight is handled several times during transit—loaded, unloaded, and transferred at terminals. If packaging and palletizing aren’t done correctly, shipments can shift, get damaged, or even be rejected by the carrier. Poor packaging can also lead to costly claims, delays, and missed guaranteed delivery windows.
How to Avoid It
-
Use sturdy, high-quality pallets – A strong pallet helps distribute weight evenly and supports the load during transit. Make sure the pallet is in good condition and appropriate for your shipment’s total cubic inches and weight.
-
Shrink-wrap and secure freight properly – Wrapping shipments tightly with stretch film and using straps or banding helps prevent movement and damage. If stacking, ensure weight is evenly distributed and avoid overhanging items that could be damaged or cause instability.
-
Label freight clearly – Misrouted shipments often happen due to unclear or missing labels. Ensure every pallet is marked with the correct destination, handling instructions, and tracking information to avoid mix-ups at terminals.
-
Choose the right packaging – Using other packaging, such as edge protectors, corner boards, or cushioning materials, can help protect fragile goods and reduce impact damage.
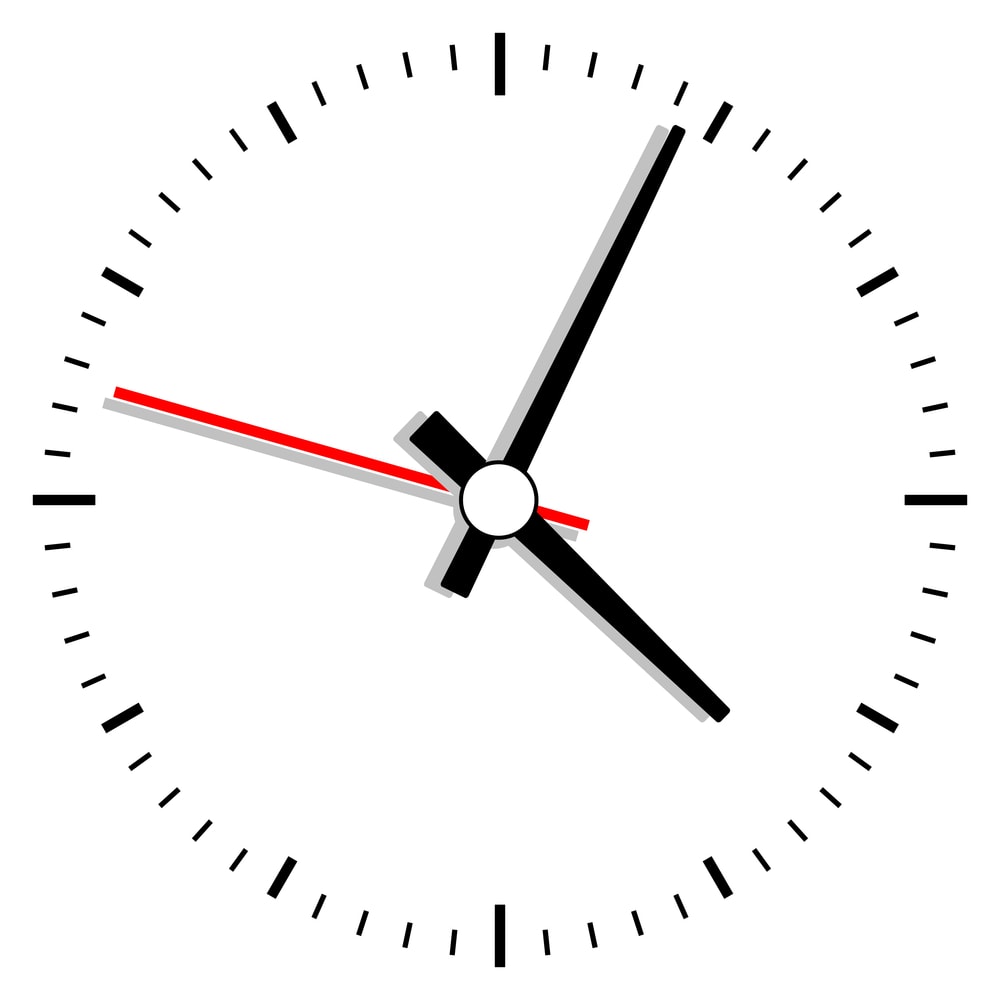
Mistake #4: Not Scheduling Pickup & Delivery Properly
Timing is everything when shipping LTL freight. Unlike full truckload shipping, LTL carriers handle multiple freight shipments at a time, meaning delays and extra fees can occur if pickup and delivery aren’t planned correctly. Failing to account for special services—such as liftgate delivery, inside pickup, or limited-access delivery—can result in unexpected charges, missed delivery windows, and frustrated customers.
How to Avoid It
-
Know your pickup and delivery requirements before booking – Determine if your location needs a liftgate, residential delivery, or any other special handling. Some LTL freight shipments require appointments, especially in high-security or limited-access areas.
-
Request special services in advance – If your freight requires non-standard services, notify the carrier upfront to avoid surprise fees. Many LTL carriers charge extra for services not included in the initial booking.
-
Confirm transit times with the carrier – LTL freight moves through multiple terminals, and delays can happen. Verify estimated transit times and coordinate with your carrier to ensure your shipment arrives on schedule.
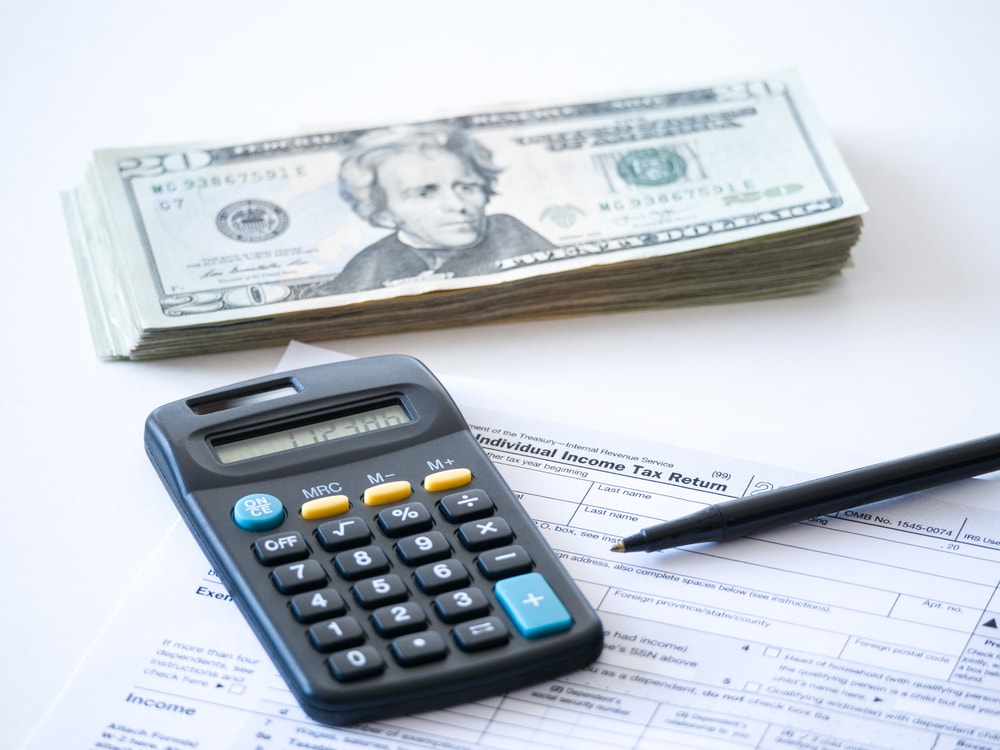
Mistake #5: Ignoring Accessorial Charges
When shipping LTL freight, many businesses focus on base rates but overlook accessorial charges—fees applied for services beyond standard pickup and delivery. LTL carriers charge for additional services like residential delivery, inside pickup, limited-access locations, and liftgate requirements. Failing to account for these charges can lead to unexpected costs, throwing off your shipping budget and reducing profitability.
How to Avoid It
-
Understand common accessorial fees – Charges for LTL shipments can include residential delivery, limited-access locations (such as construction sites or schools), and liftgate service for locations without a dock. Knowing these costs upfront helps you avoid surprises.
-
Factor accessorials into your shipping budget – If your shipments frequently require additional services, build these costs into your pricing strategy to prevent budget overruns.
-
Work with a logistics provider that offers upfront pricing – A freight partner with transparent pricing can help you accurately estimate costs, ensuring no hidden fees disrupt your LTL freight shipping expenses.
Avoid LTL Shipping Mistakes with the Right Partner
LTL shipping doesn’t have to be complicated. At ShipEX Logistics, we help shippers avoid costly mistakes, optimize freight class, and manage LTL shipments with transparency and efficiency.
Whether you need rate negotiation, freight classification guidance, or end-to-end LTL management, ShipEX has the expertise to streamline your shipping operations.
Contact ShipEX Logistics today to get a competitive LTL shipping quote and avoid the headaches of hidden fees and shipment delays.